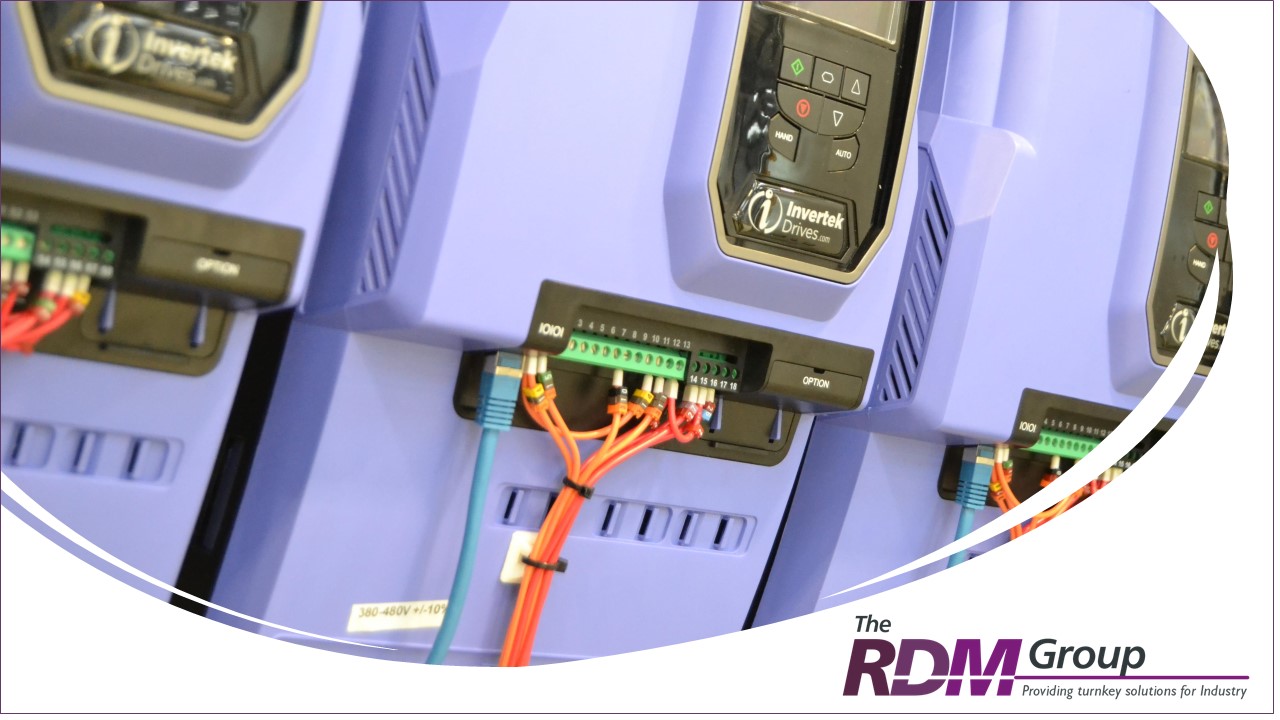
Its widely understood and accepted that reducing pollution and creating a greener environment is both essential and the way forward. Even if you don’t totally agree with this statement or the current methods been used to provide a greener environment, it is hard to argue that saving energy is a bad thing.
Governments all around the world have introduced energy saving targets and are putting legislation and regulations in place to ensure they meet those targets.
While individuals can help reduce energy usage and CO2 emissions simply by changing the way we live and the waste we produce, the biggest savings need to come from the industry sector, and from improved control in commercial buildings rather than the domestic sector. Together these are estimated to account for more than half of the energy consumption currently used worldwide.
One way that industry can contribute to saving energy, is with energy efficient motor control using a variable speed drive (VSD) also known as an inverter.
Inverters are amazing bits of kit designed to save energy when running a motor in any application. However far too often inverters are used incorrectly and for the wrong reasons. Inverters are very complex things which would be very difficult to explain in a short blog like this, however the principal energy saving techniques are very easy to explain.
There are two ways to benefit from efficient motor control using an inverter. They are designed to reduce the energy needed to start a motor and reduce the amount of energy used when the motor is running at the desired speed.
Motor Start Up
When you start a motor with a direct on line (D.O.L) starter the motor is just switched on with all the power thrusted at the motor at once, and the motor tries to start a full speed instantly. As a result of this, it uses up to 8 times more energy to start the motor than is required to run the motor when it gets momentum and is running at full speed. This is deemed acceptable for smaller motors but its still a waste of energy which comes at a cost to both the user and the environment.
Using a star delta starter for larger motors is very common. A Star delta is basically without getting technical an assisted start. The motor starts in star using low torque and less energy until it gets to full speed and then switches over to delta where it can run at full speed until stopped. This method uses around 1/3 of the energy at start up. While that sound great the process from start up to full speed can take a little as 6 seconds depending on the motor, so the saving isn’t great and is probably more beneficial to the motor than the environment and your wallet.
An inverter gradually winds up the motor for longer and as a result uses less energy for longer therefore saving the amount of energy used to start the motor. Not only is this a great saving on the consumption of energy but is very useful if the buildings mains supply is not big enough to start large motor using the conventional star delta method, or if you have lots of motor starting at the same time.
Full Running Speed
Inverters may well be a cost saving and a more environmentally friendly way of starting a motor, but the real benefits are in the savings when running a motor for long periods.
This is where most companies get it wrong. If you buy for example an 11kW, 3Ph, 400v, 50Hz motor and you run it at full speed, then you will not be saving much if any energy, or financial cost because a 50Hz motor running at 50Hz uses the same amount of energy regardless of the method of control.
Far too often when we carry out installations of these products, we are installing inverter panels to run motors for various applications at their full load current which kinds of defeats the whole process of using an inverter.
In a perfect world in this example, you would buy a larger motor and slow it down with the use of a variable speed drive (VSD). It sounds so simple, and it is. Because the motor is not working as hard to produce the same output as an 11kW motor, it’s using less energy. Less energy means less financial impact on your balance sheets and is better for the environment.
Variable Speed Control
Another great reason for using a VSD is the ability to reduce or increasing the speed of a motor when required. If you are moving a product or several products using one motor then a VSD can change the amount of power required to keep the motor running at the same speed dependant on the amount of product been moved. Ultimately this mean that the motor doesn’t need to be run at full speed all the time which is another way of consuming less energy and reducing the running costs of the machine(s).
The Financial Benefits
Its impossible to put an exact amount on this because each application is different, the usage can differ as well as your energy costs. If your particular application is designed correctly and the calculation are worked out as accurately as possible then the energy cost saving can be massive. In some cases, we have known customers energy saving to pay off the purchase of there equipment in as little as three years.
The downside to this is that the purchase of the initial equipment is likely to cost more, the cost of an inverter is much higher than the conventional D.O.L or Start Delta methods, and the increased size of motor which also required the increased size of the inverter all add up, but the running costs of your equipment will be dramatically reduced. The purchasing cost will soon be forgotten but the running cost is a permanent fixture for as long as your machine is running, so a saving in the running cost should be looked at as newly generated profit.
To help with the burden cost of purchasing inverter drives the government are issuing grants to companies that proceed down this avenue. The grants cover between 50-80% of the cost of purchasing so this must be a big help to the old purse strings.
Our Experience
At RDM we have a vast amount of knowledge and experience in inverter drives. 70% of the panels designed and manufactured at RDM Controls have one or more variable speed drives in them. When it comes to installing them, there is a little more required in the commissioning than just turning it on and our engineers are the right team with the right knowledge to ensure the maximum efficiency.
We have access and pricing structure on most VSD manufactures, and we are able to incorporate and install your preferred choice.
What’s on the Market?
All the big manufactures have VSD for every occasion in their ever-growing catalogue list of switch gear. The list of applications and variety of drives is endless and confusing to many, but all very essential to the type of application it was designed for.
At RDM we like to use the Invertek range. Not only do they look stunning with their purple fronts, but they have proven to be very reliable too. I would describe them as a mid-price ranged product providing excellent value for money.
For more information on Inverter drives and other control panel related queries visit our website www.rdm-group.co.uk or call our team on 01484 660503
Government Grants https://www.westofengland-ca.gov.uk/business/green-business-grants/